This section has been enriched with detailed answers to common questions, offering insights into the versatility, design process, and unique applications. By providing these detailed responses, we aim to empower our customers with the knowledge they need to make informed decisions about gloss stickers and labels.
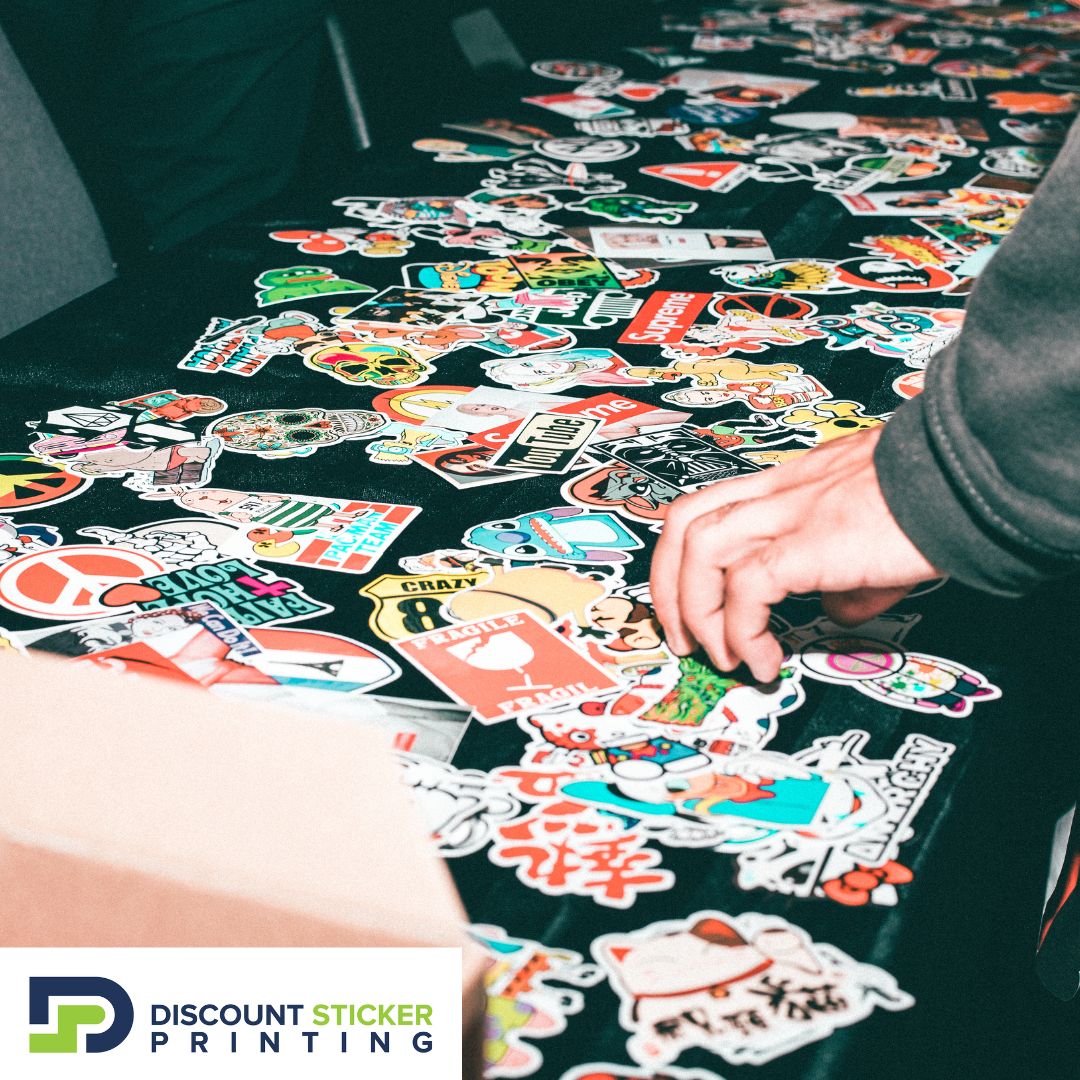
What are Gloss Stickers?
Gloss stickers and labels have a shiny, reflective surface that’s the opposite of non-reflective matt. It’s the most popular type of sticker as the finish works well with the vast majority of designs, making the colours look intense and vibrant.
They can also come in any shape and size, along with a range of specialist materials including metallic and clear, allowing them to be tailored to any kind of application.
Benefits of Gloss Stickers & Gloss Labels
The primary benefit of gloss stickers is their shiny aesthetic. They come equipped with a smooth, reflective surface that catches the light and draws the attention of potential customers, making a memorable first impression.
The glossy surface also allows colours to reflect the light better, making them more vivid. It also makes black appear deeper and more crisp. This is in contrast to matt, where these colours can look more subdued and pastel-like by comparison.
By utilising state-of-the-art Indigo printing technology, we can guarantee the most distinctive and memorable finish for all your gloss stickers.
Common Uses of Glossy Stickers & Labels
One of the most common uses of gloss stickers is for product labelling, which can range from food and drink, to candles, to cosmetics, to toiletries, to supplements and more.
They typically work best when the surface they’re applied to (such as packaging) is also glossy. This creates a continuation of the shiny finish across the front of the whole product for a more professional look.
Gloss stickers are also widely used for promotional purposes, too. For example, if an office-based company was attending a conference, they might bring along reusable water bottles, coffee mugs, pens and stationery to promote their services. A glossy sticker on the front of these items provides instant branding at an affordable price.
Another common use is for merchandising. Clubs, societies and bands can sell or give away their own stickers to help with promotion.
Types of Gloss Labels & Stickers
We offer gloss stickers crafted from either weatherproof vinyl polypropylene, or more cost-effective paper, depending on how your stickers will be used and the kind of aesthetic you want to achieve.
Polypropylene is more durable and hard-wearing with UV and tear-resistant properties, while paper stickers are more cost-effective and still work well in most applications.
Specialist materials are also available in gloss, such as multi-colour metallic with a foil effect, and also clear with a transparent material to blend your sticker or label into the background surface.
When it comes to size and shape, the choice is entirely up to you, as we offer printing in any shape and size with your own measurements.
Applying Gloss Stickers
Tips for Applying Gloss Stickers
When it comes to the application of gloss stickers, precision is everything. The adhesive used on the back of our stickers is designed for longevity, so do not press down until you have the label in the exact position you desire.
Once you do this, holding each side of the sticker with each hand, press down firmly in the middle of the label. Smooth the sides down evenly, removing any air bubbles that may have appeared.
Ensuring Proper Adhesion and Longevity
While the stickers and labels can be made to handle most types of conditions comfortably, including hot, cold and wet, overall longevity can be increased by storing the stickers in a cool, dry place until they’re ready to be used.
Keeping sheets/singles stored flat, and rolls properly wound, will also minimise the risk of warping and creasing to maximise adhesion when it’s time to apply them.
Removing Gloss Stickers
If the time has come to remove your gloss sticker, it’s worth bearing in mind that Polypropylene is easier to remove due to it being tear-resistant, so it will typically all come off in one piece. Paper, on the other hand, can have a tendency to rip when doing so.
Typically no residue will be left behind, but if there is any due to the nature of the surface, this can be scraped off while taking good care with the surface to avoid damage.
Glossy Sticker Pricing and Ordering
Factors Affecting Gloss Sticker Prices
The material you choose will impact the price of your gloss stickers. Polypropylene is a more expensive material due to its extra durability and waterproof nature, but if you don’t require this, then paper can be a more budget-friendly option with equally good print quality.
Other pricing factors include whether you’d like gloss lamination for an extra layer of protection and extra shine. Having them supplied on rolls is also our cheapest option, but sheets or individually-cut singles are available for a little extra.
Getting a Quote for Gloss Stickers
For an instant price, simply enter your desired size and shape into the pricing calculator above, then select the options on the next page for an exact price based on your specifications. You can also continue this process to order online in minutes.
If you have a design in mind but aren’t sure how to create it, just select our design service during checkout and we’ll create bespoke artwork for you based on your instructions.
Recommended shapes and sizes:
Use Case. | Recommended Shape | Ideal Size (cm) |
Logo Stickers | Circle or Square | 5cm x 5cm |
Bumper Stickers | Rectangle | 25cm x 7.6cm |
Product Labels | Oval or Rectangle | 10cm x 5cm |
Laptop Decals | Custom Shapes | 8cm x 8cm (Varies) |
Window Stickers | Circle or Square | 15cm x 15cm |
Address Labels | Rectangle | 7cm x 5cm |
Promo Giveaways | Any Shape | Custom |
Ordering Gloss Stickers Online
For one of our experts to talk you through your order on the phone, please call 01302 288 577. You can also use live chat or email to talk with one of our advisors.
Alternatively, you can order directly online in minutes by selecting your specifications, uploading your artwork (or choosing our design service) and then completing payment.
When uploading your own artwork, ensure you are using high-resolution images and have considered the size and shape of the stickers you would like to receive.
When selecting your colours, we suggest CMYK colour mode for the crispest, clearest finished result.